
欧姆龙通过导入新的环境管理会计方法“材料流量成本会计=MFCA※",发现了以前生产费用计算中不曾看见的损耗,进行了改进:同时,通过开发划时代的成形技术,实现了节约资源和能源。(※MFCA:Material Flow Cost Accounting德国的经营环境研究所(IMU)开发的环境管理会计的方法2000年在日本经济产业省的环境管理会计方法研究项目中首次被介绍到日本)
从财务角度实现制造过程损耗的“可视化’
欧姆龙从2006年度起开始导入“MFCA”。MFCA是一种环境管理会计的方法,与传统的生产费用计算相比,制造过程中所发生的损耗在计算方法上有所不同。过去只把不良品的制造成本作为损耗,而MFCA除不良品之外,把下脚料以及不必要的待机用电量等成本也作为损耗。即对原材料、能源的流量和库存进行跟踪,从数量与金额两个方面找出损耗的发生之处。
通过“可视化”找出的损耗在MFCA中被称为“负产品”。通过改进工序,尽可能减少这类负产品,以实现资源与能源的节约。
MFCA的原型产生于德国,在日本,作为日本经济产业省千禧年项目的一项内容,2000年以后开始应用于企业。欧姆龙从2006年度起,由集团环保活动的核心部门“生产革新本部”主导,开始在全公司范围内导入MFCA。首先,在集团内部招募了示范工厂。当时集团整体的产量正在逐年增长,废弃物的产生量也在不断增长。
生产过程中产生的大部分废弃物一般都来自零部件加工厂。因此,将从事开关和传感器等电子零部件加工的欧姆龙仓吉股份公司(鸟取县)确定为示范工厂,先行导入了MFCA。
通过MFCA得以“可视化”的成本
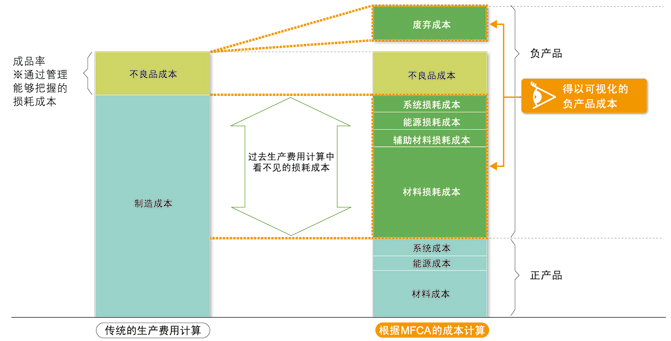
成品率:制造过程中原材料等投入量中实际被使用到产品的量
不良品之外的其他损耗 一一从这里发现新的改进潜力
欧姆龙总部的生产革新本部和欧姆龙仓吉公司的零部件制造团队组成了MFCA项目小组,于2006年5月选择产量最大的微动开关生产线开始了最初的改进活动。
首先在全部生产线中,找出原材料被加工、其状态发生变化的工序。再通过测量原材料重量,来分别把握每一工序上投入了何种原材料、投入多少、其中废弃多少、又有多少进入下一个工序。这样可以精确掌握在什么工序产生了多少损耗。
调查结果相当惊人。投放到生产线的原材料中最终作为成品下线时的重量只剩下大约28%,也就是说,竟然有70%以上的原材料都被废弃了。
迄今为止,传统的生产费用计算只考虑了不良品的损耗,而为降低不良品率,也在不断地改进。但是到了不良品发生率已被降至1-2%的今天,可改进的余地已经非常有限了。而现在通过对原材料流程的细致调查,我们又发现了新的损耗——不良品之外的废弃原材料,这里还存在着很大的改进空间。这一发现令技术人员们振奋不已。
通过在生产现场进行的各种改进措施,欧姆龙仓吉公司的废弃物发生总量比上年同期减少了11%(年62t) o
开关的制造工序
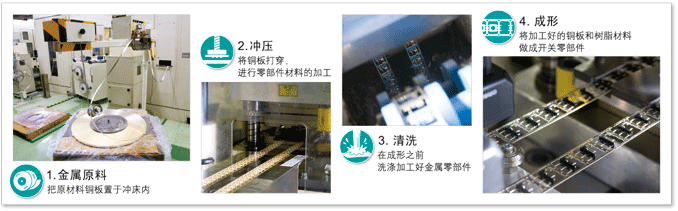
通过MFCA欧姆龙仓吉取得的改进效果
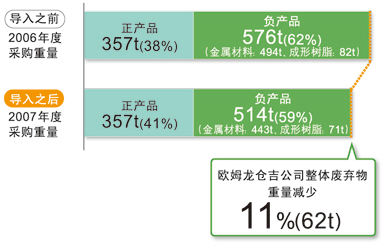
消减“可视化”后的原材料损耗,实现了节约资源
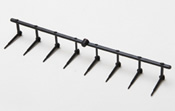 树脂材料的连接框部分
2006年度通过MFCA“可视化”,发现欧姆龙仓吉公司的“负产品”的重量达到576t。为了削减这个重量,项目小组最先着手的是冲压加工工序中所产生的铜板废料堆。这个工序中,宽2cm的带状铜板打孑L加工后,能成为零部件的部分还不到一半。由于打孔后的铜板都变成了废料,因此首先为减少这部分废料认真地进行了重新设计。将1排打孔变为2排,打孔的间隔也缩为最短,并且将材料连接之处所产生的损耗降到最小,这样就削减了32%的铜废料。
此外,在其他工序中将带状铜板转到下一工序时需要将铜板卷到细长的滚轴上。卷取的铜板两端在下一工序中被当做边角料废弃。对这一问题的解决是,通过将8片铜板连接延长,并将卷取滚轴改为大滚筒式,减少了边角料。而且,也将卷取后铜板的交换次数从75分钟1次减少到每10个小时1次,即减少到原来的1/8,从而大幅度减少了生产损耗。
接下来的成形工序中,树脂材料的连接框成为关注点。塑料模型中,连接框是指连接零部件之间的框框部分。连接框只被切取使用必要的一部分,其他的部分都被扔掉了。项目小组通过尽可能缩小连接框部分的模具设计,削减了17%的体积。这样虽然模具的成本增加了,但通过减少树脂的消耗量,总的成本还是减少了。
此外除了改进采购材料和设备之外项目小组也进行了工作方法的改良。之前每个工人所产生的废弃物数量大不相同,但通过制定详细的操作程序,并将其标准化后,无论谁操作都不会产生偏差,将废弃物控制到了最小程度。
通过铜板改良削减废料
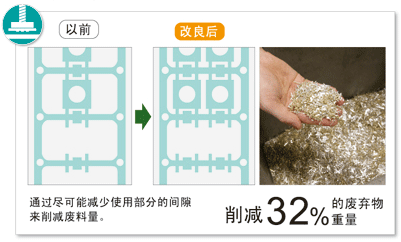
通过改良材料卷取机来减少交换次数
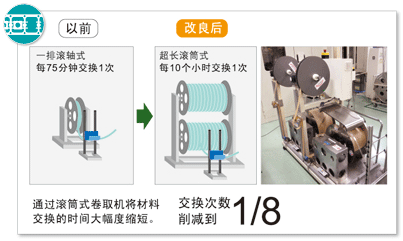
|
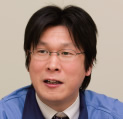 通过MFCA看到的损耗程度令现场大为振奋
欧姆龙仓吉株式会社
生产统括部 零部件制造Group
谷口 孝弘
过去我们虽然也注意到有很多原材料都变成了废料但以重量和金额准确掌握每个工序中的损耗这种想法在引进MFCA之前确实没有过。自从公布了曾经高达70%的损耗之后员工们一下子有了动力:“原来还有这么大的改进空间啊!”一旦损耗可以看见就可以马上开展改进活动了。
不仅仅是原材料在电力消耗的“可视化”方面MFCA也发挥了很大作用。因此今后我们也将在资源的有效利用以及C02减排方面不断扩大MFCA的应用。
|
|
将MFCA的改进成果推广到日本及海外的工场
生产革新本部
后量·环墙中心
原田 圣明
欧姆龙至今为止已经开展了多项减少废弃物的活动现在又在把欧姆龙仓吉公司的MFCA成功经验逐步推广到其他生产基地。目前MFCA已在日本4个生产基地以及海外1个生产基地得到应用各个基地通过改进活动都取得了成效。
欧姆龙的质量·环境中心负有向日本和海外的生产基地推广MFCA损耗“可视化”及改进经验的重要使命。同时如何将MFCA的应用成果推广到其他不同制造工序的产品上也是一项重要任务。欧姆龙今后还将继续充分利用MFCA推进集团整体的节约能源资源的工作。
|
打破常规,通过“1秒成形”大幅度减少原材料和能源消耗
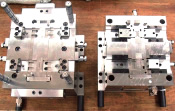 1秒成形中重要的连接
框热模具。利用它大幅
度缩短了成形时间
公司总部生产技术部门的工程技术中心也针对零部件制造成形工序中的损耗开展了削减技术的研发,这就是打破常规、对“1秒成形”技术的实用化所进行的挑战。
树脂构件是将加热的液体树脂灌入模具制作而成,将其冷却凝固至少需要5秒,这是业界的常识。但是,我们考虑如果不生产制作连接框,只是直接灌入树脂生产制作零部件部分,就可以缩短冷却时间。
工程技术中心与成形机制造商通过反复研究改良实验机器,终于在通用型标准机器上实现了“1秒”的成形时间,这种机器在大量生产的工场也可以投入使用。由此,大幅度削减了原材料和能源,如果进行成本换算,相当于平均制造1个零部件节省资源达到70%以上。
"1秒成形”技术目前已在日本的2个生产基地开始应用计划于2010年起在海外生产基地推广使用。
减少能源消耗量的挑战 一一将活动扩大到日本及海外的其他基地
欧姆龙仓吉公司的改进不仅仅停留在削减废弃物上,2008年度该公司利用MFCA方法进一步开展了减少能源消耗量的活动。与测量废弃物重量相同,这次精确测量各个加工工序中的使用电量以及生产状况的变化,将其“可视化”,从而发现了设备待机和停止时使用电量的浪费。现在,该公司通过改进运用方法及设备来减少这些浪费。此外,还对成形工序中的操作时间和使用电量进行测量,通过各处细致地削减损耗时间可以缩短3成以上的成形时间。这样,能源消耗量随之减少成形生产线也从3条减为2条。
欧姆龙仓吉公司通过导入MFCA,过去看不到的损耗能够以数值的形式显示出来,从而可以确实掌握需要改进之处。同时,由于可以看到新的改进潜力,现场士气高涨,员工们更加积极地参与了改进活动。欧姆龙仓吉公司过去也进行了多次的生产现场改进活动,而通过MFCA的应用取得了更大的成效。
欧姆龙仓吉公司获得的节约能源资源的经验与技术正在向欧姆龙其他基地推广。今后,欧姆龙将充分利用MFCA加快推进集团整体的节约能源资源的事业。 |